PLMSync runs from your PDM/PLM system, enabling direct synchronization of Bill of Materials (BOM) data from PDM/PLM systems to ERP systems.
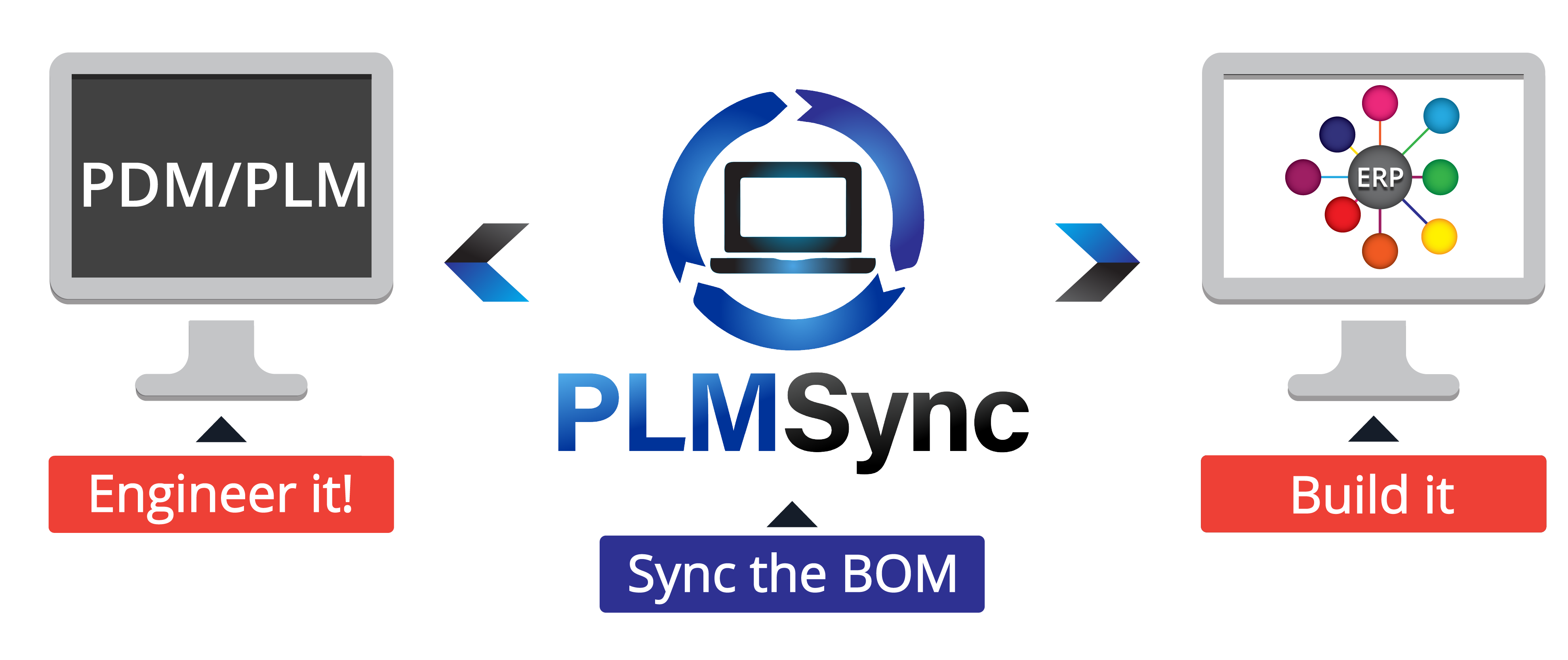
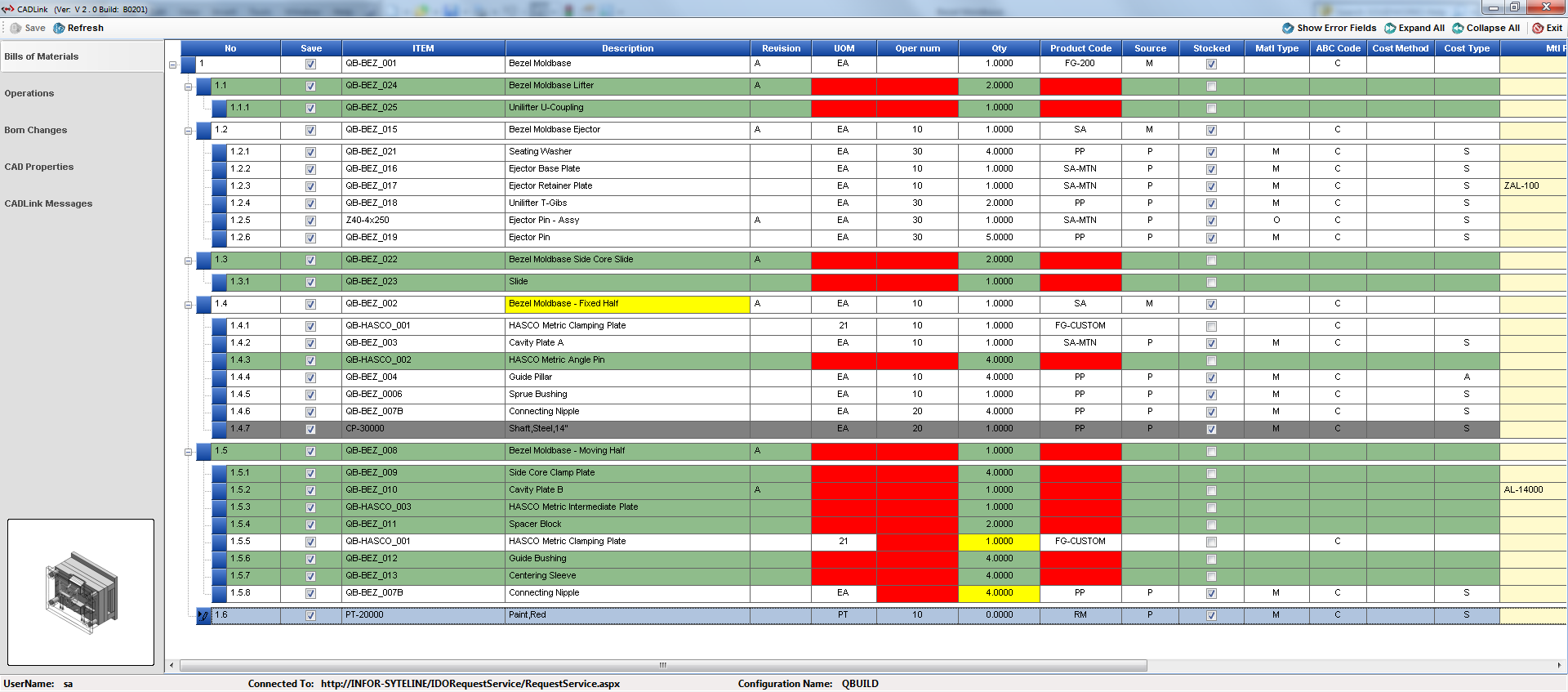
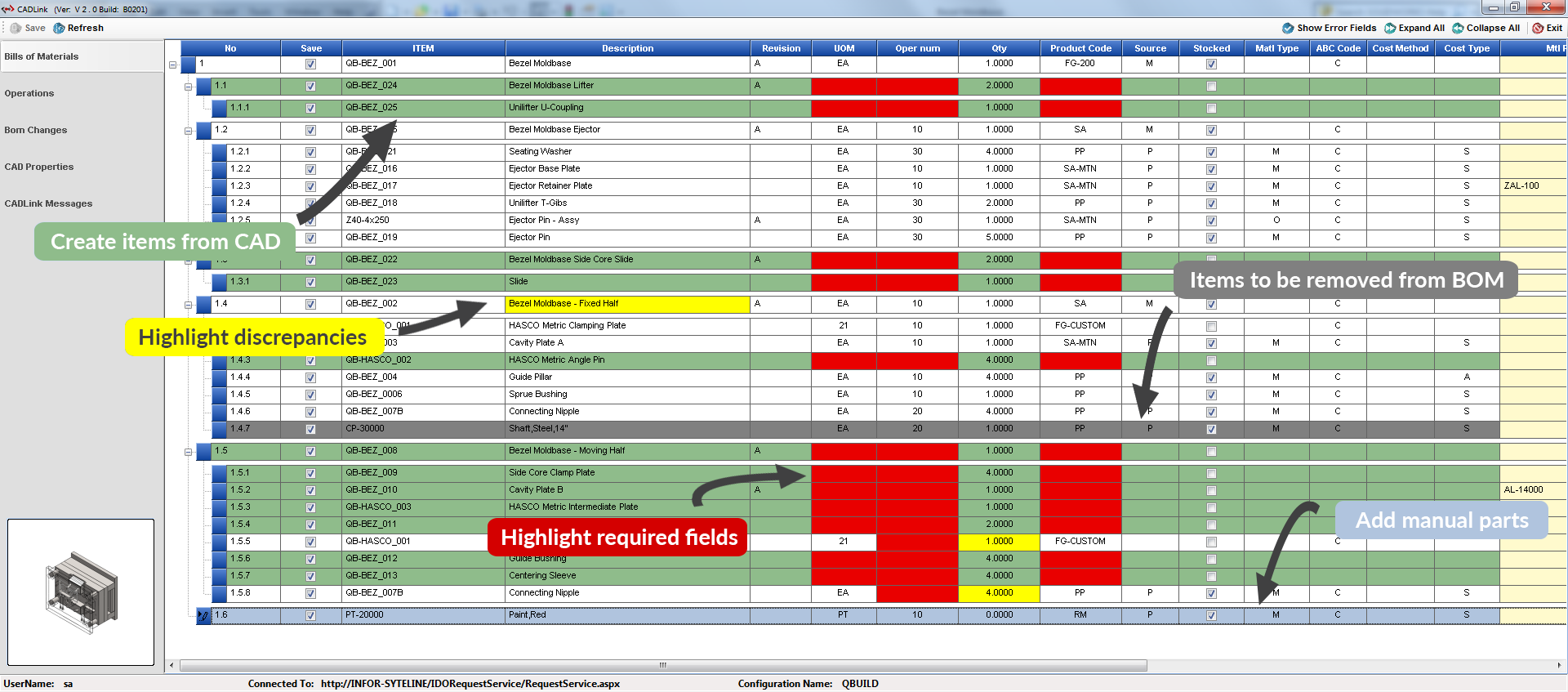
- Real-time, bi-directional link connecting your PDM/PLM and ERP system
- Directly interfaces BOM and Part information within PDM/PLM solution
- Comparison between PDM/PLM and ERP data with comprehensive feedback on the results
- Comprehensive routing interface
- Effortlessly integrates with QBuild’s ECx Manager
- Full Effectivity date functionality for precise data management
- Can be integrated with any CAD, PLM or ERP system
Eliminate ERP Clerical Work
PLMSync empowers your engineering team to concentrate on their core strengths—engineering. By eliminating double and triple data entries, engineering information seamlessly enters both your PDM/PLM system and ERP system through a unified interface. Creating new items in the item master is effortlessly streamlined as PLMSync extracts data from the PDM/PLM system and pushes it to the ERP system.
Free up your engineering staff to focus on impactful engineering work and reduce overall engineering costs. Minimizing the time spent on manual data input across multiple platforms allows them to invest more time in projects and designs. PLMSync enhances efficiency and productivity, letting your team thrive in their primary expertise.
Reduce Data Entry Errors
When manually entering data into two distinct databases, the likelihood of discrepancies increases, often arising from typos or mistakes, especially when Engineers are required to fill numerous fields for each assembly, subassembly, and part. PLMSync addresses this challenge by unifying the data entry process, effectively eliminating sources of error in transferring data between your PDM/PLM and ERP system.
This unified approach not only enhances accuracy but also presents a significant cost-saving opportunity. A single mistake in the Bill of Materials can potentially lead to ordering errors, resulting in scrap, excess inventory, or delayed shipment of parts. PLMSync eliminates these risks, ensuring a streamlined and error-free data transfer process with consequential benefits for overall operational efficiency and cost management.
Drawing Accuracy and Consistency
The PLMSync Interface guarantees that the details on the drawing, descriptions, and revisions match exactly with the information in your ERP ensuring accuracy in drawings minimizes confusion and decreases errors on the shop floor caused by conflicting information between work orders, sales orders, and drawings. This alignment greatly reduces waste and saves on engineering costs by cutting down the need for clarification. The outcome is a smoother and less error-prone manufacturing process.