What to consider when deciding between a PDM or CAD integration with ERP
Bringing your BOM information into ERP is a bottleneck where the process needs to be accurate. Otherwise you risk downstream issues such as production delays, purchasing inaccuracies, and wrong builds. Many manufacturers use Computer Aided Design (CAD) software for modeling and drafting, as well as a Product Data Management (PDM) system to store and manage product data from design to production.
So having an integration between Engineering (CAD and PDM) and Manufacturing (ERP) is a no-brainer. Through our many years of experience, we know that it is better to keep it simple with a single integration point from either CAD or PDM. So when it comes to a tool like CADLink, how do you decide which approach works best for you?
It depends on your processes, your needs, and how you use each of these systems. That’s why we’ll be going over the main features of both CAD and PDM integrations, as well as the pros and cons of each.
The most basic thing that sets these two types of integrations apart is where you launch CADLink from. A CAD integration is built directly as an add-in into the design software, so a user would need to launch CADLink from their CAD software. On the other hand, a PDM integration means you would launch CADLink from the PDM software instead of from the design.
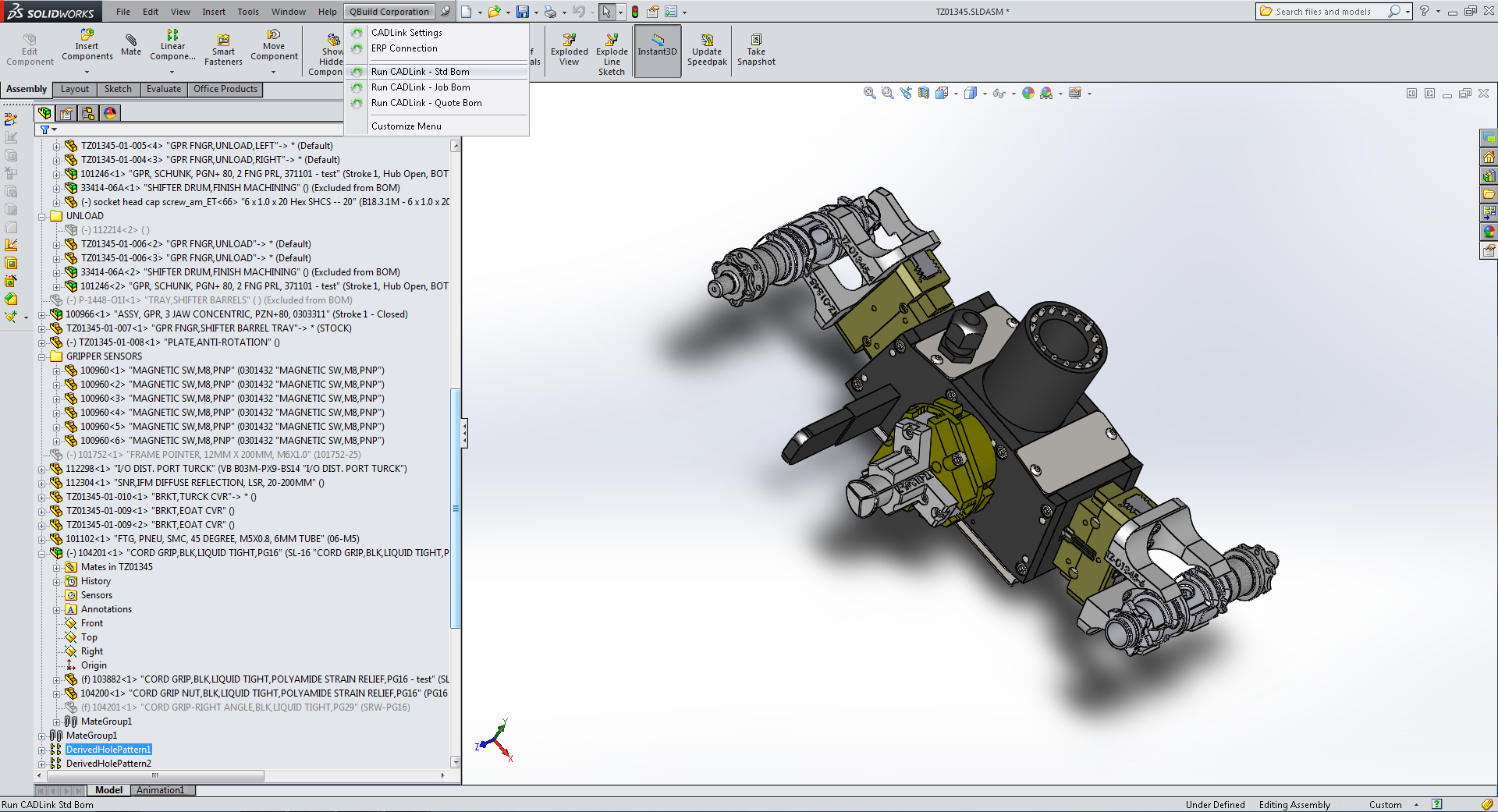
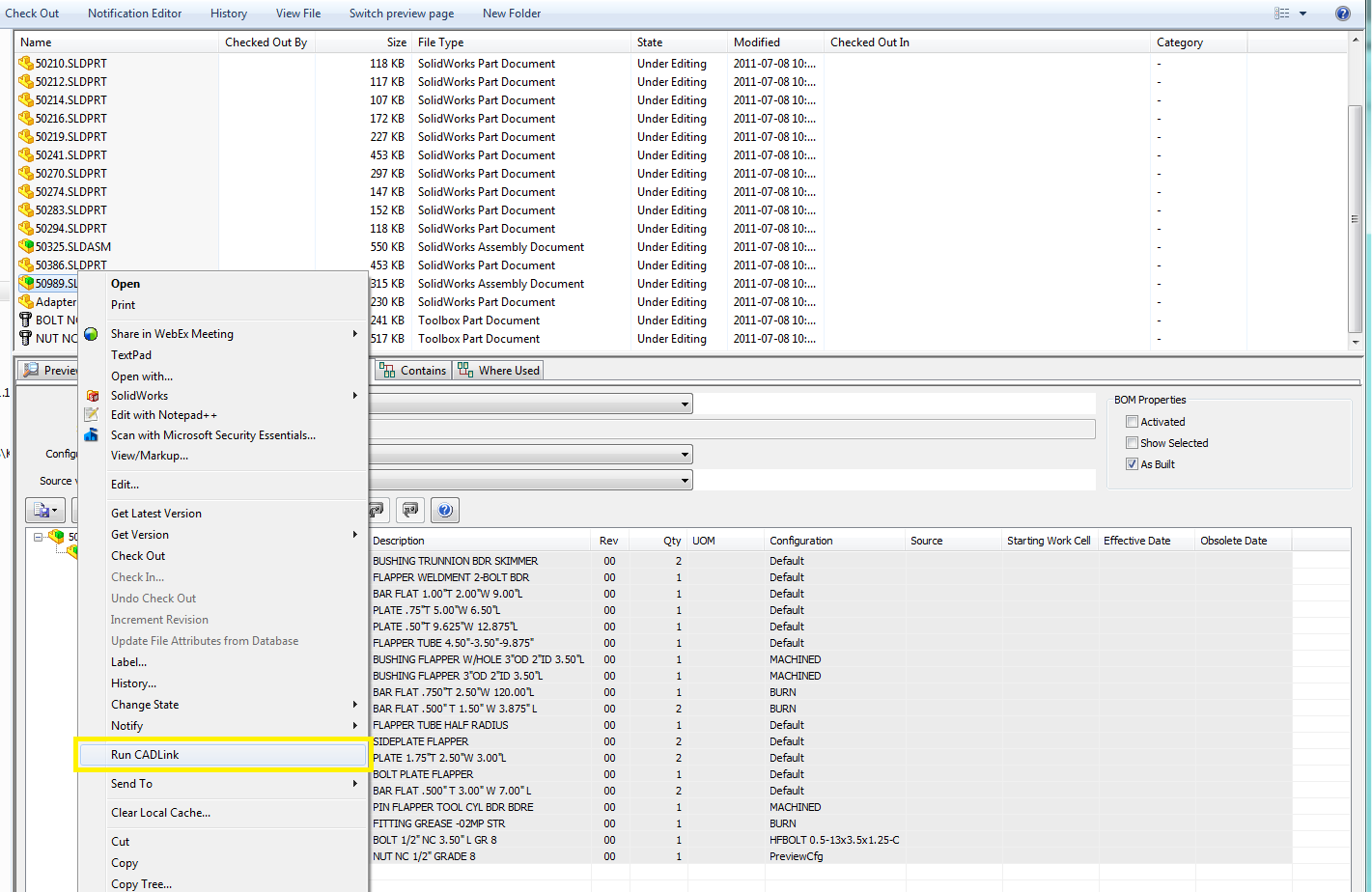
In order to understand the more detail-oriented differences between a CAD integration and a PDM integration, we need to look at how they differ and how they interact with each other.
The CAD Integration
The 3D CAD software is where the engineer creates the drawings, the parts, and assembly designs. While doing so, a lot of information is entered about each part, including part numbers, descriptions etc, and create a bill of material structure that production depends on. All of this metadata is kept in the CAD properties and files which get pushed to ERP with CADLink at the click of a button.
A CAD integration is most commonly used by the design engineers themselves. This allows CADLink to be used by the people who know the most about the particular BOM. With CADLink, the engineer can review all the data that will be saved to ERP, and make good use of the data validation that CADLink runs to ensure that the information is accurate; changes that are needed can be made directly in the CADLink interface and saved back into the CAD data.
The great thing about integrating with CAD is that you can have partial BOM pushes. If your design engineers are the ones who are responsible for pushing the BOM to ERP, CADLink is a great tool to assist them with getting all the data into ERP. Partial BOM pushes are a great advantage because it allows you to get those long lead time items into ERP ahead of time.
On the other hand, some data may not be included in your CAD files when the integration syncs the BOM, like routing information. This means that a CAD integration may not have all the required information to put in the ERP for production to commence.
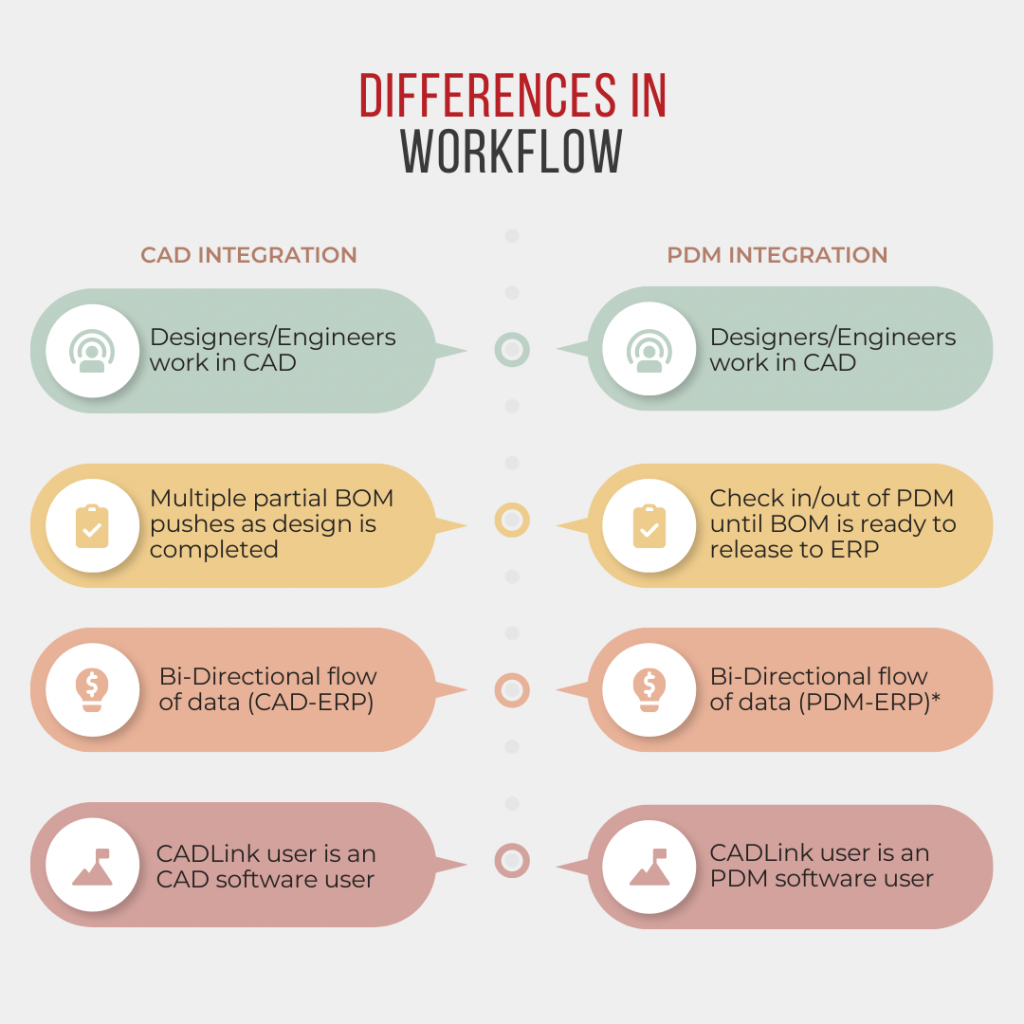
The PDM Integration
While CAD may contain some important data, many companies opt for a PDM system to help assist with managing these files. PDM systems are designed to help you, as Neil Cooke from Onshape explains,
‘manage and organize the complex interdependencies that CAD creates between each type of file’.
It’s possible you may have routing and other information that a team outside of your engineering department needs to assign. Customers may prefer having that group make use of CADLink, instead of the designers, to push the BOM and assign routings or additional data at the same time, so that once the data is in ERP, production already has all the information they need to begin.*
PDM typically has much more data available than what is saved into the CAD files. This means, whatever data PDM has, CADLink will be able to make use of as well to help ensure that your ERP contains all of your latest, most accurate information.
An integration with PDM lets CADLink ensure that only an approved BOM is sent to your ERP, based on the approval process that is set up in your PDM. A PDM CADLink integration has the ability to check the state of the assembly to make sure that it has gone through this approval process, and prevent premature data pushes if the design has not yet been approved.
However, this stricter control of data can be limiting, as some PDMs do not allow for bi-directional data transfer**. This means that any changes that you want to make after the approval process must be made in your CAD or in PDM and resubmitted for approval. There may be changes that are necessary, but the PDM user is not as knowledgeable or doesn’t have all the information regarding the BOM in comparison to the original design engineer.
Conclusion
Overall, there is no one best answer for everyone. Processes are not completed the same way in every company, and we wouldn’t expect it to be. Each company has their own processes and even functionality is used in different ways. Your best option when making this decision, is to examine what you need out of an integration to your ERP, and figure out what type of integration is best fit to your process, your design process, team responsibility, and data flow.
*Not all integrations have routing functionality available, please contact [email protected] if you have questions regarding a particular PDM integration
**This is dependent on the PDM system, not all integrations are restricted to one-way transfer.