Don’t Settle for the Export-Import
The fancier alternative to manual entry, but with its own set of problems.
Getting your BOM data into your ERP can be a strenuous and time-consuming process. In another article, we discussed the reasons manufacturing companies shouldn’t homebrew their CAD-ERP integration solution. This blog is a follow-up, diving into the most common way the process is homebrewed or custom developed by other VARs, and why it fails.
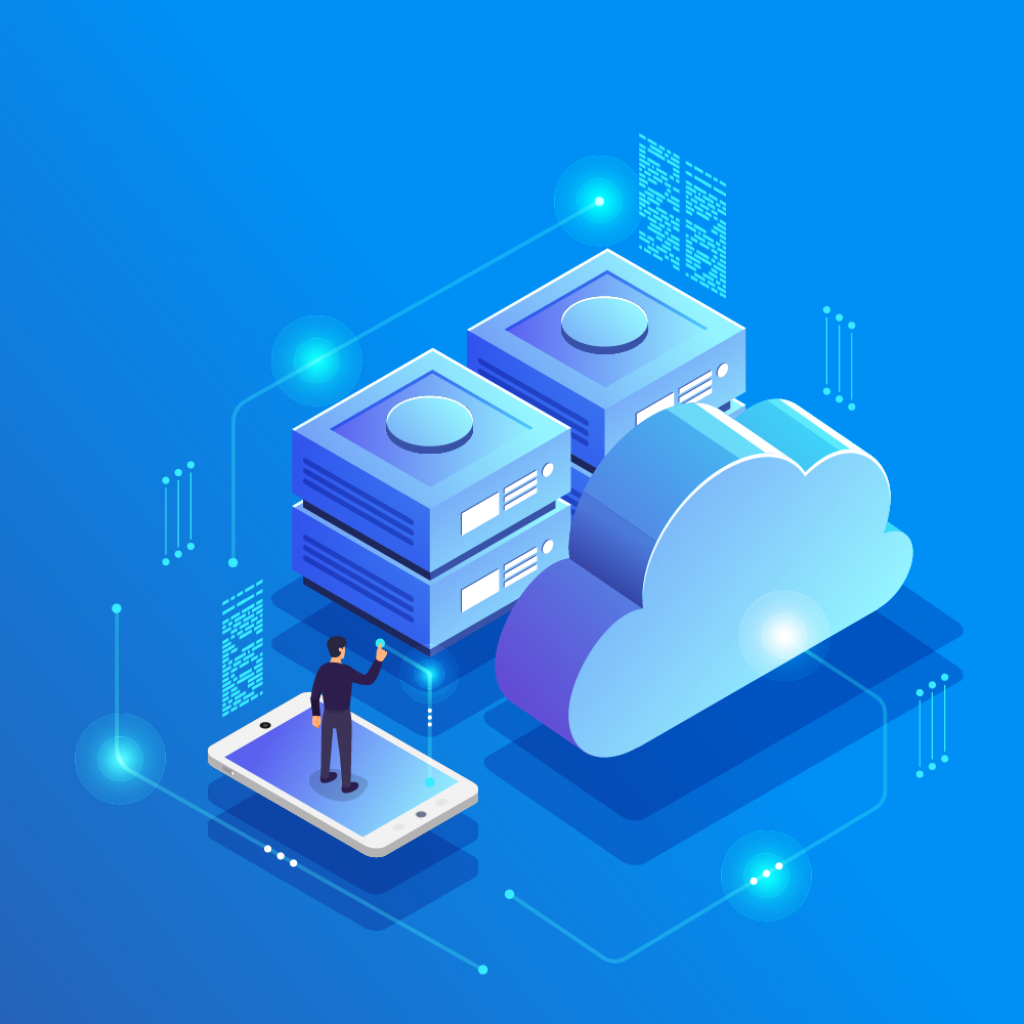
What is the Export-Import?
The Export-Import, otherwise known as “the two-step”, is a process where the Bill of Materials (BOM) data from CAD, PDM, or PLM is exported into a .csv or Excel format (most commonly). Then, it is imported into your ERP database to “create” the new parts and BOMs. On the surface, this sounds attractive to users looking for a CAD-ERP integration. Users aren’t manually keying the BOM data to ERP, and involves a perceived low software cost.
But in QBuild Software’s 15+ years of experience of integrating Engineering BOM data to ERP, we’ve seen how manufacturing companies have suffered being encumbered by this process. Sometimes they are taking even more time than those still keying BOMs into ERP manually.
Here are 3 points to consider before committing to an Export-Import solution.
Data massaging – the type of massage that isn’t relaxing
“Massaging the data” is all the prep work you’ll have to do, arranging the exported data into the format the ERP accepts. With all the varying CAD and ERP systems available (and all the varying versions), what are the chances your ERP import format matches your CAD’s export? Zilch. So in order to bridge the gap, users still have to spend time deleting columns and rows, manually fetching data from ERP, applying formulas, and running macros in order for the import file to be ERP-ready. If you don’t get it right the first time, you’ll spend more time troubleshooting it or worse, pushing data to wrong tables (see point #2). Depending on the change, you may have been better off entering it manually!
There is none of that with CADLink. As a partner and/or solutions provider for over 35 engineering applications and 36 ERPs, our solution comes ready to connect any combination of those systems. CADLink takes care of pulling all the relevant details from both the CAD and ERP to compare and visually display the differences, then pushing the new and updated data back to those systems into the right places. The user can rest easy knowing this is all taken care of.
You’ll be flying blind (no data validation)
By importing your BOM data directly from an export, you’re opening the door for users to write engineering BOM data directly to the ERP’s database tables. This is a high-risk scenario. Tools to do the data transfer are not sophisticated enough to validate the requirements for each field. If there are errors on the BOM (missing information/null values, character strings too long, wrong values, etc.), they will not be caught and will be written to the ERP database. Even worse, it may overwrite existing data in the ERP with this erroneous data. All this leads to more errors for users further downstream or even a full database corruption in your live environment.
Ditch the risk and go with CADLink. Since we partner with ERP providers, our development team works with theirs to build fully a certified solution. Before CADLink pushes the data to ERP, it loads a visual comparison of sets of data from CAD and ERP, highlighting all the differences between the two and providing the functionality to review and make changes. CADLink validates each field that it updates, ensuring that field requirements are satisfied. On top of that, we utilize the ERP’s Application Programming Interface (API), whenever provided, which further provides a layer of validation and ensures data is transferred as expected by the ERP solution.
Pick a Bi-Directional Solution
The simplest reason not to go two-step is you’re not going to be able to write back changes to the CAD system. Once data is exported from CAD, any changes you make there onward will not make it back to the CAD unless someone manually makes the matching change. This includes any corrections such as typos and errors applied to the exported file, or any relevant data from the ERP added you want to send back to CAD. If you only correct data being sent to the ERP, you’ll inevitably end up with discrepancies between the CAD and ERP, leading to manufacturing errors, and time-consuming confusion later on.
CADLink is a fully bi-directional solution, featuring a live, simultaneous connection to the CAD and ERP system. It highlights and shows where any data is not the same between matching part records in both systems and provides an intuitive interface to reconcile the differences. Then, any changes made in the CADLink interface (i.e. changing descriptions, assigning raw materials) can be pushed bi-directionally, so the matching sets of data are pushed to both systems and stay in sync.